PDCA循环作为持续改进与质量管理的核心工具,如何助力个人与组织实现螺旋式提升?本文从底层逻辑到实战场景,带您全面掌握这一科学方法。
一、PDCA的起源与核心价值
PDCA循环由美国统计学家沃特·休哈特提出,后经戴明博士在日本推广并完善,因此被称为“戴明环”。其本质是通过“计划(Plan)—执行(Do)—检查(Check)—处理(Act)”四个阶段的循环迭代,实现问题的持续解决与质量的阶梯式提升。
核心特点:
闭环思维:每个环节紧密衔接,形成“发现问题→解决问题→固化经验”的闭环。
动态优化:如爬楼梯般逐步升级,每一轮循环解决部分问题,未完成项进入下一循环。
全员参与:适用于个人目标管理、团队协作及组织战略落地。
二、PDCA的核心阶段与八大步骤解析
1. 计划阶段(Plan)
目标设定:遵循SMART原则(具体、可衡量、可实现、相关性、时限性),例如“3个月内客户投诉率下降30%”。
问题分析:
使用鱼骨图、5W2H法挖掘根本原因(如设备故障导致交货延迟)。
聚焦关键因素,采用二八法则筛选20%的核心问题。
方案制定:明确5W1H要素(Why/What/Where/Who/When/How),如“每周三质检团队检查生产线”。
2. 执行阶段(Do)
任务拆解:将计划转化为每日TODO清单,例如“市场部在5月前完成100份用户调研”。
过程记录:建立数据采集机制,如生产日志、客户反馈表,便于后续分析。
3. 检查阶段(Check)
效果评估:对比目标与实际数据,例如“新流程使生产效率提升15%,但次品率未达标”。
根因追溯:通过对比执行偏差,识别计划缺陷或执行疏漏。
4. 处理阶段(Act)
标准化成果:将有效经验固化为操作手册,如修订《设备维护标准》。
遗留问题转译:将未解决的20%问题纳入下一循环,如“优化供应商管理流程”。
三、PDCA的实战应用场景与案例
1. 制造业:生产线质量提升
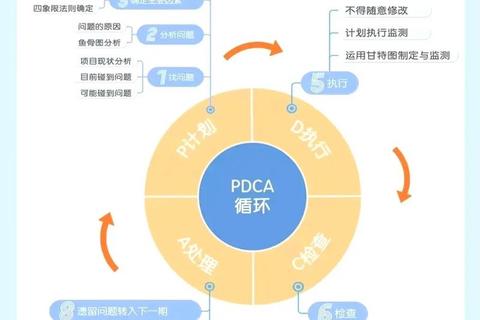
案例:某汽车零件厂通过PDCA将次品率从8%降至2%:
Plan:分析发现模具磨损是主因,制定模具周检计划。
Do:培训质检员使用新型检测工具。
Check:次品率下降但局部工序仍超限。
Act:引入自动化检测设备并启动下一循环。
2. 服务业:客户满意度优化
案例:连锁餐厅减少投诉的PDCA实践:
Plan:通过问卷锁定“上菜速度慢”为关键问题。
Do:优化厨房动线,推行电子点单系统。
Check:平均上菜时间缩短5分钟,但高峰期仍滞后。
Act:增加兼职员工排班表,进入新一轮循环。
3. 个人成长:学习目标达成
Plan:设定“6个月通过PMP认证”目标,拆解为每月学习章节。
Do:每日投入1小时学习,每周模拟测试。
Check:发现风险管理章节得分偏低。
Act:调整学习重点,加入线上专项培训。
四、PDCA高效落地的5大实用建议
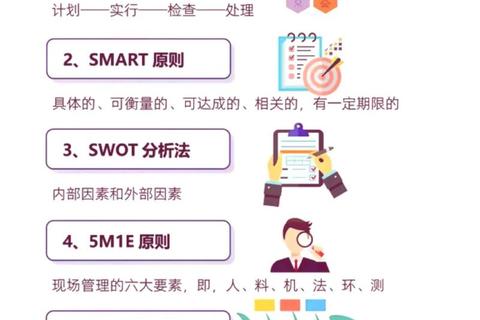
1. 可视化工具应用
使用甘特图跟踪进度,用看板管理标注问题节点(如Trello、Jira)。
推荐工具:Boardmix等白板软件绘制PDCA流程图。
2. 数据驱动决策
建立关键指标(KPI)体系,例如“客户重复购买率”“项目延期率”。
避免主观判断,用数据验证假设。
3. 跨部门协同机制
定期召开复盘会,邀请执行层与决策层共同参与(如月度质量分析会)。
案例:某医院通过多科室PDCA联动,将患者等待时间减少40%。
4. 灵活应对变化
预留10%资源应对突发情况,如市场需求突变时快速调整生产计划。
采用滚动式计划,每季度更新目标。
5. 文化渗透策略
将PDCA纳入员工考核,奖励“最佳改进案例”。
高层示范:CEO亲自参与质量改善小组,传递持续改进理念。
五、常见误区与避坑指南
计划空洞:避免“提高服务质量”等模糊目标,改为“客户投诉响应时间<2小时”。
检查缺失:警惕“重执行轻评估”,需设定阶段性检查节点(如每周五数据复盘)。
标准化不足:成功经验未及时固化,导致同类问题反复发生。
PDCA不仅是工具,更是一种持续精进的思维方式。无论是企业战略升级,还是个人职业发展,掌握这一循环逻辑,都能在动态变化中构建核心竞争力。正如戴明所言:“质量不是检验出来的,而是改进出来的。”通过每一轮PDCA的扎实落地,组织与个人终将在迭代中迈向卓越。