倒模技术作为一种高精度复制工艺,正逐步成为制造业、科研及艺术领域的关键工具。本文将全面解析其核心原理、应用场景及操作流程,并提供实用建议,帮助读者深入理解这一技术的价值与实现路径。
一、倒模技术的基本定义与核心原理
倒模技术是通过制作原型或模型的复制品,将其表面细节转移到模具中,再利用模具生产出与原型高度一致的制品。其核心在于“复制-转移-成型”三步流程,适用于塑料、金属、陶瓷、硅胶等多种材料。例如,在微纳加工中,PDMS(聚二甲基硅氧烷)凭借高弹性和化学稳定性,成为复制微米级结构的首选材料。
技术特点:
高精度:可复制纳米级细节,如芯片上的微流道。
多材料兼容:硅胶、树脂、金属等均适用。
效率与经济性:适合小批量快速生产,降低研发成本。
二、倒模技术的应用场景
1. 工业制造
微纳器件生产:PDMS倒模用于制造微流控芯片,应用于生物检测、药物筛选。
精密零件复制:如汽车发动机部件的快速原型开发,通过倒模缩短模具制造周期。
塑料制品批量生产:瓶盖、家电外壳等通过倒模实现高效注塑。
2. 影视与艺术领域
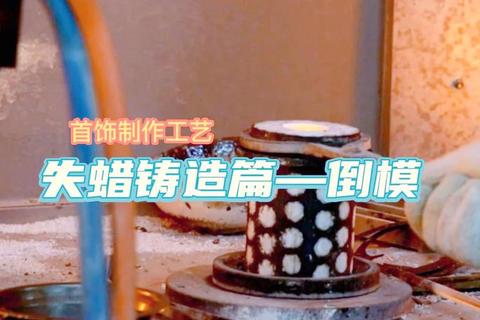
特效道具制作:硅胶倒模可复制演员面部特征,用于外星人或老年妆等特殊造型。
文物复制:石膏倒模技术用于复原雕塑细节,保护珍贵文化遗产。
3. 医疗与科研
人体器官模型:通过硅胶倒模制作手术模拟器,帮助医生练习复杂操作。
生物兼容器件:PDMS倒模的微流控芯片可用于细胞培养与药物测试。
4. 消费电子
高外观要求产品:如手机外壳采用倒装模技术,避免表面浇口痕迹,提升美观度。
三、倒模技术的制作流程详解
步骤1:原型设计与表面处理
原型材料选择:金属、光敏树脂或3D打印模型均可作为母版。
抗粘处理:对硅模板喷涂TMCS(三甲基氯硅烷),防止PDMS粘连。
步骤2:模具材料配置与脱气
混合比例:PDMS与固化剂通常按10:1混合,机械搅拌后真空脱气以消除气泡。
材料替代方案:硅胶适合复杂曲面,树脂则用于高硬度需求场景。
步骤3:浇铸与成型
浇铸技巧:缓慢倾倒材料至模具边缘,避免气泡产生(图5)。
旋涂工艺:针对薄膜结构(如微流控芯片),通过匀胶机控制厚度至微米级。
步骤4:固化与脱模
温度控制:80℃烘烤2小时可加速PDMS固化,厚件需延长至4小时。
脱模工具:使用刀片从边缘切入,配合氮辅助分离。
四、倒模技术的挑战与解决方案
1. 微纳结构的复制难点
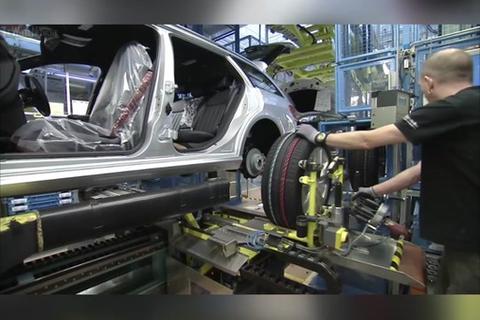
问题:200nm以下结构易断裂,高深宽比特征填充困难。
解决方案:采用紫外纳米压印技术,或优化PDMS混合比例增强弹性。
2. 脱模失败风险
预防措施:
模具表面喷涂氟化剂降低粘附力。
设计倒装模顶出机构,实现自动化脱模(如螺纹芯柱旋转顶出)。
3. 材料收缩与变形
控制方法:
添加玻璃纤维增强树脂抗变形能力。
分阶段固化:先低温预固化,再高温强化。
五、实用建议与操作技巧
1. 材料选择指南
硅胶:适合复杂曲面,但需注意丙酮环境下的溶胀问题。
光敏树脂:推荐用于3D打印原型,精度可达0.02mm。
2. 温度与时间控制
PDMS固化温度每升高10℃,时间可缩短30%,但超过100℃易导致脆化。
3. 成本优化策略
小批量生产使用硅胶模具,大批量切换至金属模以降低单件成本。
4. 现代技术融合
结合3D打印快速制作母版,缩短原型开发周期。
六、总结与未来趋势
倒模技术正朝着更高精度(纳米级复制)、智能化(自动化脱模系统)及环保化(可降解模具材料)方向发展。对于从业者而言,掌握材料特性与工艺细节,结合新兴技术(如AI驱动的模具设计软件),将是提升竞争力的关键。无论是科研实验室还是制造企业,合理运用倒模技术,都能在效率与成本之间找到最优平衡点。