在质量管理与生产优化领域,PPK(过程性能指数)是衡量生产过程实际表现的重要指标。它不仅是企业评估短期生产能力的工具,更是发现问题、优化流程的关键依据。本文将从概念解析、计算方法、行业应用及优化建议等维度,全面解读PPK的核心价值。
一、PPK的定义与核心逻辑
PPK(Process Performance Index)用于量化生产过程在实际运行中的表现能力。其核心逻辑是通过比较产品特性的实际分布与规格要求,判断过程是否满足质量目标。
关键要点:
适用场景:
试生产阶段(如新产品验证)。
过程不稳定或存在特殊原因变异(如设备调试、材料批次差异)。
短期数据分析(如小批量生产)。
与CPK的区别:
PPK反映实际表现,包含普通原因和特殊原因变异;CPK仅评估稳定状态下的潜在能力,仅考虑普通原因变异。
PPK计算使用总体标准差(σ_total),CPK使用组内标准差(σ_within)。
公式表达:
[ PPK = minleft(frac{USL
mu}{3sigma_{total}}, frac{mu
LSL}{3sigma_{total}}right) ]
其中,USL为上规格限,LSL为下规格限,μ为过程均值,σ_total为总体标准差。
二、PPK的核心价值与适用场景
1. 生产初期的质量验证
在试生产阶段,PPK用于快速评估新工艺或设备的可行性。例如,某汽车零部件厂商通过计算PPK发现某零件的加工能力不足(PPK<1.67),进而优化模具参数,最终将PPK提升至2.0以上。
2. 不稳定过程的监控
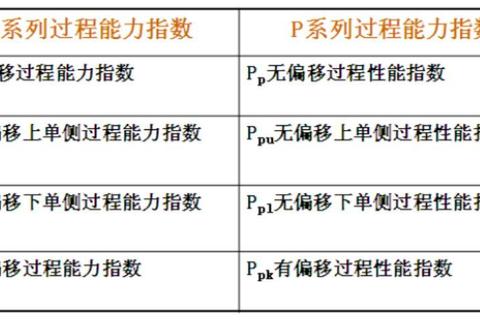
当生产过程存在不可控因素(如原材料波动、设备老化)时,PPK能真实反映整体性能。例如,某医药企业通过PPK分析发现某药品灌装工序的变异来源,最终通过改进环境控制使PPK达标。
3. 短期数据评估
对于小批量生产或紧急订单,PPK无需长期稳定数据即可快速得出结论。例如,某电子企业使用PPK评估某芯片封装工序的短期能力,确保首批产品合格率。
三、PPK与CPK的协同应用策略
1. 数据驱动的差异分析
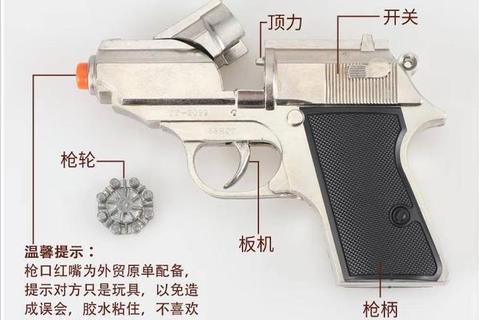
当PPK显著低于CPK:表明存在特殊原因变异(如操作失误、设备故障),需优先排查。
当PPK接近CPK:说明过程稳定,普通原因变异是主要问题,需系统性改进(如工艺参数优化)。
2. 工具组合提升效率
控制图:监控过程稳定性,识别异常点。
直方图:可视化数据分布,辅助判断PPK是否达标。
Minitab等软件:自动计算PPK并生成分析报告,减少人工误差。
四、行业应用案例与启示
1. 制造业
案例:某刹车片生产商发现PPK值低于1.33,分析发现设备温度控制不稳定。通过加装温控传感器,PPK提升至1.5。
启示:设备维护与参数标准化是提升PPK的关键。
2. 医药行业
案例:某药企通过PPK分析发现某批次药品的灌装量波动过大,根源是环境湿度超标。改进后PPK从0.8提升至1.2。
启示:环境控制与操作流程标准化对高精度行业尤为重要。
3. 食品行业
案例:某乳制品企业使用PPK监控包装重量,发现某生产线称重传感器偏差。校准后PPK达标,每年减少浪费超100万元。
启示:定期设备校准与员工培训可显著降低成本。
五、提升PPK的实用建议
1. 数据收集规范
样本量要求:至少100个连续数据点,避免抽样偏差。
时间间隔:连续生产时按固定间隔取样(如每小时取5件)。
2. 过程优化方向
消除特殊原因变异:通过根本原因分析(如鱼骨图)定位问题。
减少普通原因变异:优化工艺参数(如压力、温度)或升级设备。
3. 长期监控机制
定期评估:量产阶段每季度计算PPK,对比历史数据趋势。
自动化工具:使用SPC系统实时监控,预警异常波动。
六、总结
PPK不仅是质量管理的“诊断工具”,更是企业持续改进的“指南针”。通过科学计算、工具组合与行业实践的结合,企业可以精准定位问题,降低不良率,提升客户满意度。无论是初创企业还是成熟厂商,掌握PPK的应用逻辑,都将为竞争力提升注入关键动力。